Промышленность консервативна. Любое ноу-хау — это нарушение отлаженного процесса, то есть риск. В то же время инновации повышают эффективность, помогают освоить новые рынки. Рассказываем, где промышленность черпает проверенные идеи.
Третий год такой площадкой является Промышленный конгресс инноваций и производительности IN’HUB, который проводится по инициативе «Норникеля». В сентябре 2024 года он прошёл в Мурманске и собрал руководителей инновационных проектов и экспертов из 80 компаний. На конгрессе «Норникель» представил несколько инноваций, рассказываем о двух самых важных и эффективных. А также о новом инновационном проекте.
Электролизные ванны для никеля высокой чистоты
Чтобы получить никель высокой чистоты марки High Purity (99,99%), создали специальную опытно-промышленную установку. С её помощью проводят доочистку рядового католита от оставшихся примесей железа, цинка и кобальта с помощью смол.
Ионнообменными смолами занимались давно, ещё с 2022 года. В результате долгих экспериментов подобрали смолу, которая применяется в урановой промышленности. Она оказалась эффективной для удаления примесей из никеля. Замена медной ошиновки на никелевую собственного производства, то есть изготовленную из никелевых катодов, и покрытие штанг никелем позволили снизить содержание меди в электролизере в 36 раз.
Ионнообменными смолами занимались давно, ещё с 2022 года. В результате долгих экспериментов подобрали смолу, которая применяется в урановой промышленности. Она оказалась эффективной для удаления примесей из никеля. Замена медной ошиновки на никелевую собственного производства, то есть изготовленную из никелевых катодов, и покрытие штанг никелем позволили снизить содержание меди в электролизере в 36 раз.
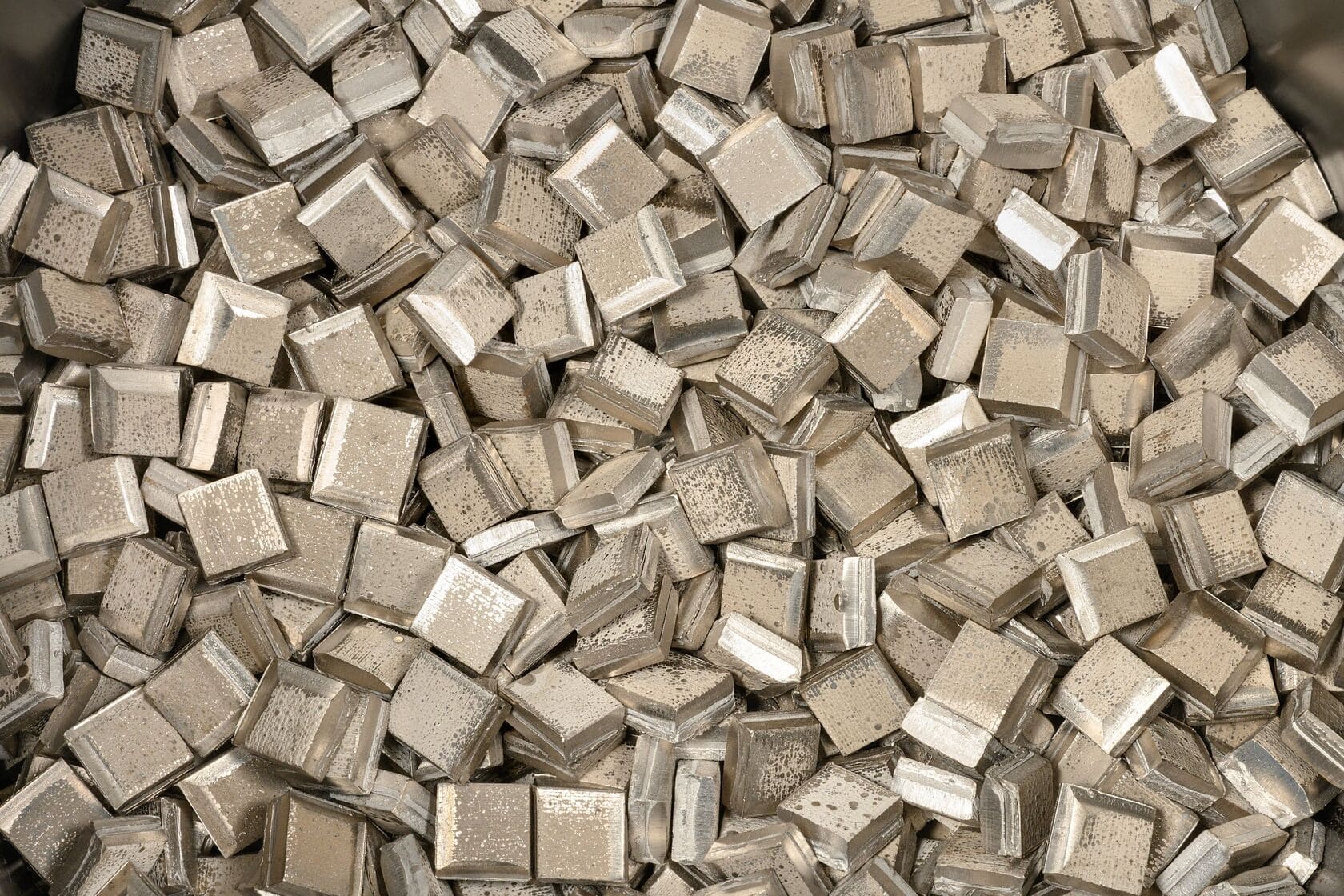
Для производства металла марки Plating Grade (99,97%) толщина катода должна быть 13−18 мм и кромка катода должна быть гладкой. Чтобы добиться этого, специалисты компании увеличили расстояние между катодом и анодом и установили рамки, экранирующие кромки катода. То есть с помощью рамок исключили неровности на поверхности и кромках катода.
Чтобы поддержать низкую концентрацию меди в электролизерах, покрыли никелем катодные штанги. Чтобы снизить содержание цинка, увеличили производительность цинкоочистки с 41 до 55 куб. м в час.
Чтобы поддержать низкую концентрацию меди в электролизерах, покрыли никелем катодные штанги. Чтобы снизить содержание цинка, увеличили производительность цинкоочистки с 41 до 55 куб. м в час.
Доход от переработки отходов производства
При производстве никеля неизбежно образуются отходы — низшие марки Н3 и Н4. В 2023 году их объём на Кольской ГМК составлял около 8%. Спроса на такую продукцию нет, а переплавлять её слишком дорого. Зато в России не хватает сульфата никеля, который нужен для аккумуляторных батареек, катализаторов, гальваники. Дефицит покрывали поставками из Китая.
Теперь выпуск сульфата никеля освоили в Кольской ГМК и планируют расширить его производство, чтобы закрыть дефицит в 2025—2026 годах.
Отходы НЗ и Н4 растворяют, затем выпаривают раствор и получают кристаллы ценного продукта. С апреля 2024 года компания продала 42 т сульфата никеля. Инвестиции в проект составили 52,2 млн руб., его потенциальный экономический эффект может составить 344 млн руб.
Теперь выпуск сульфата никеля освоили в Кольской ГМК и планируют расширить его производство, чтобы закрыть дефицит в 2025—2026 годах.
Отходы НЗ и Н4 растворяют, затем выпаривают раствор и получают кристаллы ценного продукта. С апреля 2024 года компания продала 42 т сульфата никеля. Инвестиции в проект составили 52,2 млн руб., его потенциальный экономический эффект может составить 344 млн руб.
Материалы для производства аккумуляторов
В конце 2022 года «Норникель» открыл в Санкт-Петербурге Батарейный технологический центр. Пока его разработки не были представлены на IN’HUB. Центр занимается исследованием и разработкой никельсодержащих катодных материалов (КАМ) для производства аккумуляторов.
Инвестиции в уникальное технологическое оборудование и собственные разработки составили примерно 30 млн долларов. Подобные технологии есть сейчас только в США, Германии и Китае. Качество катодных материалов Батарейного центра подтверждено независимыми лабораториями.
Команда из 40 специалистов стремится к увеличению ёмкости и стабильности КАМ. Задача-максимум — потеснить китайских производителей литий-ионных батарей, которые занимают сейчас 80% отечественного рынка.
Инвестиции в уникальное технологическое оборудование и собственные разработки составили примерно 30 млн долларов. Подобные технологии есть сейчас только в США, Германии и Китае. Качество катодных материалов Батарейного центра подтверждено независимыми лабораториями.
Команда из 40 специалистов стремится к увеличению ёмкости и стабильности КАМ. Задача-максимум — потеснить китайских производителей литий-ионных батарей, которые занимают сейчас 80% отечественного рынка.
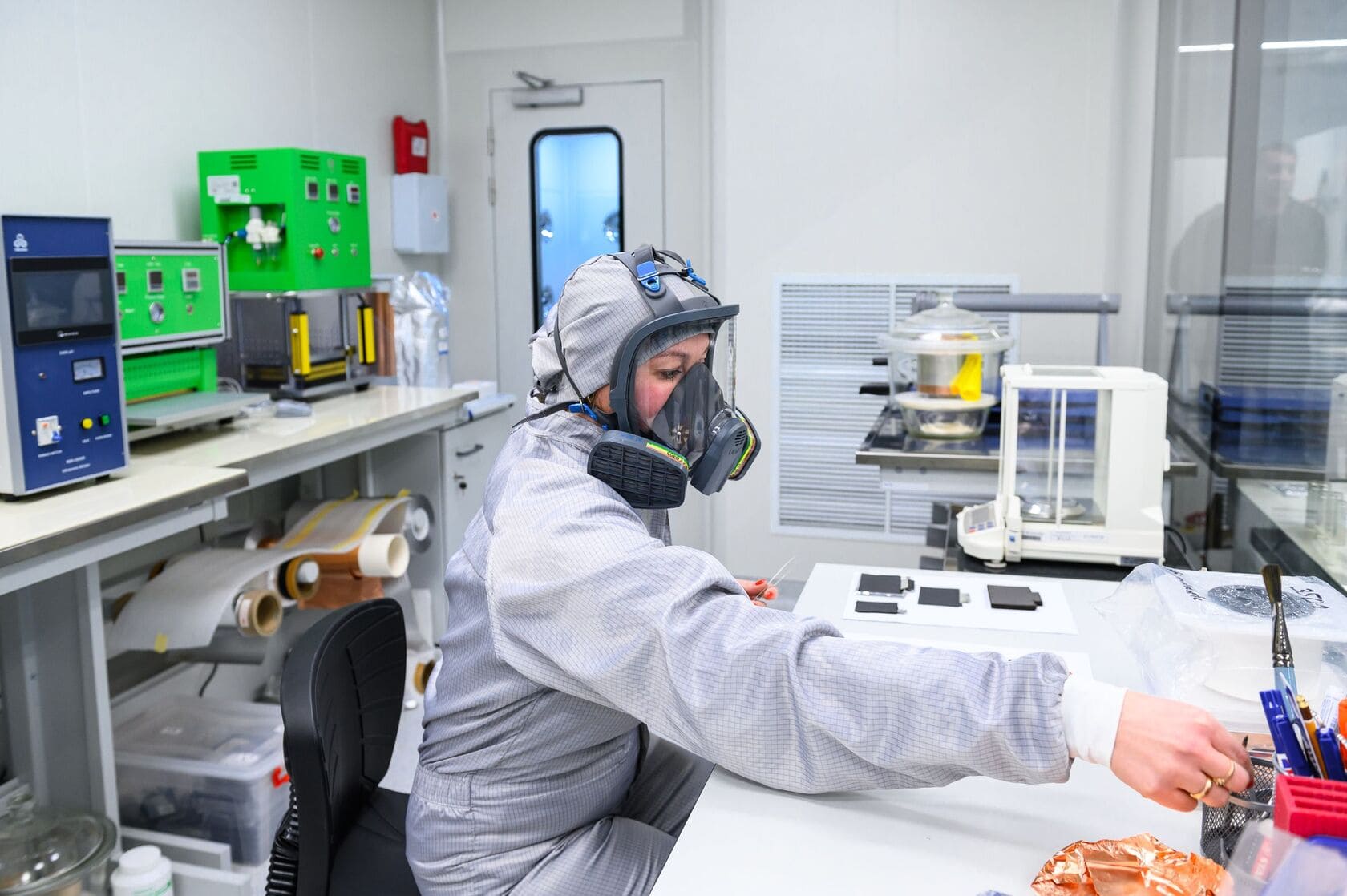
Работают в Батарейном центре и над созданием новых видов аккумуляторов, например натрий-ионных. Они лучше подходят для электромобилей в условиях российских морозов, но энергоёмкость у них пока ниже, чем у литий-ионных. В перспективе команда центра планирует разработку батарей на основе твёрдого электролита.
Производить готовые батареи «Норникель» не будет, сборкой аккумуляторов и их продажей на рынке России и дружественных стран займётся «Росатом». Компании плотно сотрудничают в этом направлении. «Росатом» уже строит в Калининградской области завод по производству литий-ионных автомобильных аккумуляторов мощностью 4 ГВт·ч в год.
Производить готовые батареи «Норникель» не будет, сборкой аккумуляторов и их продажей на рынке России и дружественных стран займётся «Росатом». Компании плотно сотрудничают в этом направлении. «Росатом» уже строит в Калининградской области завод по производству литий-ионных автомобильных аккумуляторов мощностью 4 ГВт·ч в год.
ВИТАЛИЙ БУСЬКО,
вице-президент по инновациям «Норникеля»:
"Наш Батарейный центр — самый современный. Всё, что создаётся здесь, — это результаты собственных исследований. На данный момент мы прошли два этапа: от получения десятков граммов катодных материалов за синтез до десятка килограммов.
Следующим этапом должно стать строительство пилотной установки для производства 10 т материала в год. Дальше идёт этап строительства полноценного завода, который сможет производить до 10 000 т в год.
В целом мы оцениваем потребность российского рынка в катодных активных материалах в 10 000 т к 2030 году, в то время как спрос на мировом рынке составит миллионы тонн".
Мир стоит на пороге новой промышленной революции. Внедрение инноваций, финансирование научных исследований — это вклад предприятий в собственное будущее.
Фотобанк «Норникеля»
Ноябрь, 2024
Ноябрь, 2024